Mastering Injection Mold Tool Design for Business Success
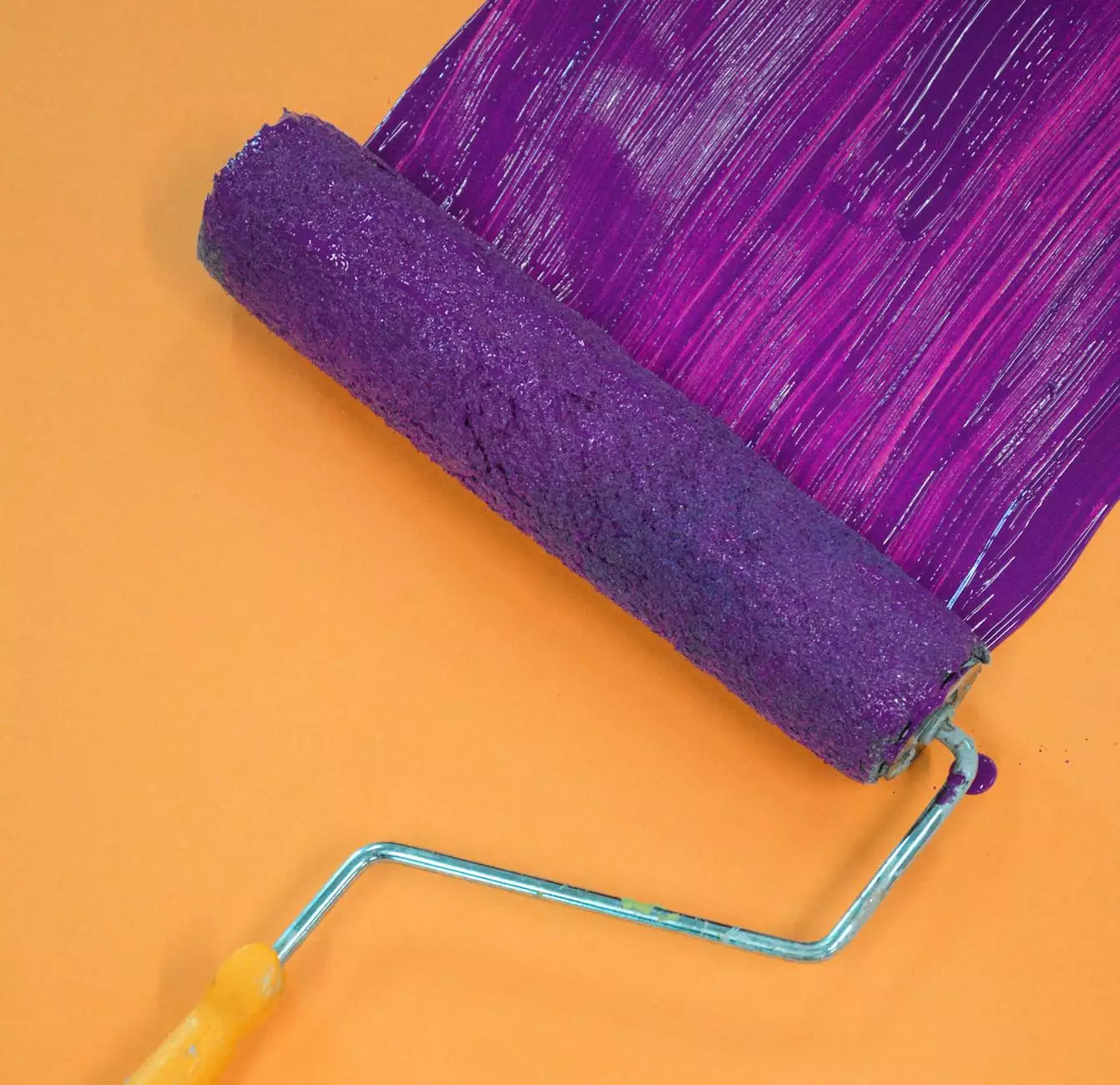
Injection mold tool design is a crucial element in the manufacturing process, particularly for businesses involved in the production of high-quality plastic parts. This article delves into the intricacies of injection mold tool design and its importance in achieving operational efficiency, product quality, and market competitiveness. With a detailed exploration of the design process, materials, trends, and best practices, we aim to provide valuable insights that can help businesses like yours soar to new heights.
The Importance of Injection Mold Tool Design
In today’s highly competitive manufacturing landscape, the quality of your products can significantly influence your brand's reputation and profitability. Injection mold tool design plays a pivotal role in this scenario. Here are some reasons why investing in proper mold design is essential:
- Enhanced Product Quality: A well-designed mold ensures precise control over product dimensions and tolerances, resulting in superior quality and reduced defects.
- Cost Efficiency: Effective mold design can minimize cycle times and maximize production efficiency, leading to lower manufacturing costs.
- Quick Market Response: Companies that invest in quality injection mold tool design can adapt to market changes quickly, producing new products faster than their competitors.
- Improved Production Rates: Optimized designs facilitate quicker production runs, allowing businesses to meet demand without delay.
Understanding the Mold Design Process
The process of designing injection molds involves several critical steps. A systematic approach not only enhances the design quality but also ensures that the molds meet the specific needs of production:
1. Concept Development
The initial phase involves understanding the product requirements, including aesthetics, functional needs, and manufacturing volume. This is where the injection mold tool design begins to take shape, with concepts created based on the product specifications.
2. Material Selection
The choice of materials for both the mold itself and the injected product is vital. Common materials for molds include:
- Tool Steel: Durable and able to withstand high pressure and temperatures.
- Aluminum: Lightweight and cost-effective for lower-volume projects.
- Composite Materials: Offering good performance for specific applications with a focus on cost reduction.
3. Designing the Mold
This phase involves detailed CAD modeling. Skilled engineers utilize advanced software to create designs that encompass all necessary aspects, such as:
- Cooling Channel Design: Efficient cooling systems are essential for maintaining cycle times and improving product quality.
- Ventilation: Proper venting ensures that air escapes during the injection process, preventing defects.
- Gate Design: Knowing where and how to inject the plastic is crucial for minimizing surface defects and ensuring uniform flow.
4. Prototyping
Creating a prototype mold allows for testing and validation of the design before full-scale production. This step is critical for identifying potential flaws and making necessary adjustments.
5. Testing and Validation
Once the prototype is developed, rigorous testing is performed. This includes:
- Functional Testing: Ensuring that the final product performs as intended in real-world conditions.
- Durability Testing: Assessing the longevity of the mold and the products it produces.
- Dimensional Testing: Verifying that all specifications and tolerances are met according to the original design.
Key Technologies in Injection Mold Tool Design
The injection mold tool design process has evolved significantly thanks to technological advancements. Here are some key technologies that have transformed the industry:
1. Computer-Aided Design (CAD)
CAD software allows designers to create precise and intricate 3D models, facilitating visualization and adjustments before physical production. This technology has dramatically improved accuracy and reduced the time needed for design iterations.
2. Computer-Aided Manufacturing (CAM)
CAM software integrates with CAD systems to automate the manufacturing processes for molds, which enhances productivity and consistency.
3. 3D Printing
3D printing technology is often used for producing quick prototypes, enabling designers to visualize and test their mold designs without the expense and time associated with traditional manufacturing methods.
4. Simulation Software
Utilizing simulation software allows teams to predict potential mold performance, flow dynamics, and cooling patterns, ultimately leading to improved design decisions.
Challenges in Injection Mold Tool Design
While the benefits are substantial, there are also challenges that businesses must navigate in the injection mold tool design process, including:
1. Design Complexity
As products become more intricate, designing molds that can effectively produce these complex shapes becomes increasingly challenging.
2. Cost Constraints
Budget limitations can restrict the selection of materials and technologies, impacting the overall quality and longevity of the molds.
3. Time-to-Market Pressure
Businesses often face tight deadlines to bring products to market, requiring efficient design and production processes without compromising quality.
Best Practices for Successful Injection Mold Tool Design
To ensure success in injection mold tool design, businesses should follow these best practices:
- Invest in Training: Continuous education and training for design teams can lead to innovative design solutions and improved efficiency.
- Maintain Open Communication: Collaboration between design, engineering, and production teams is crucial for addressing potential issues early in the design process.
- Utilize Industry Standards: Adhering to best practices and standards ensures that molds are designed for reliability and interchangeability.
- Regularly Update Designs: As materials and technology evolve, so too should your designs. Continuous improvement should be part of your business model.
Future Trends in Injection Mold Tool Design
The landscape of injection mold tool design is continuously evolving. Here are some trends to watch that could shape the future of the industry:
1. Sustainable Materials
With increasing pressure to adopt sustainable practices, more manufacturers are exploring biodegradable and recyclable materials for both products and molds.
2. Automation and Smart Manufacturing
The integration of AI and automation into the design and production processes is set to revolutionize efficiency, accuracy, and production rates.
3. Enhanced Customization
The demand for personalized products continues to rise, prompting a shift towards molds that can accommodate quick changes and custom designs.
Conclusion
In conclusion, mastering injection mold tool design is essential for any business involved in manufacturing. By understanding the design process, embracing technological advancements, and applying best practices, businesses can significantly enhance their product quality and operational efficiency. As the industry continues to evolve, staying informed about new trends will help your company maintain a competitive edge in the market.
For more information on injection mold tool design and how it can benefit your business, consider partnering with experienced mold makers like DeepMould.net. Their expertise in metal fabrication and mold design is unmatched, offering you the best support in your manufacturing journey.