CNC Turning Parts: Revolutionizing Metal Fabrication
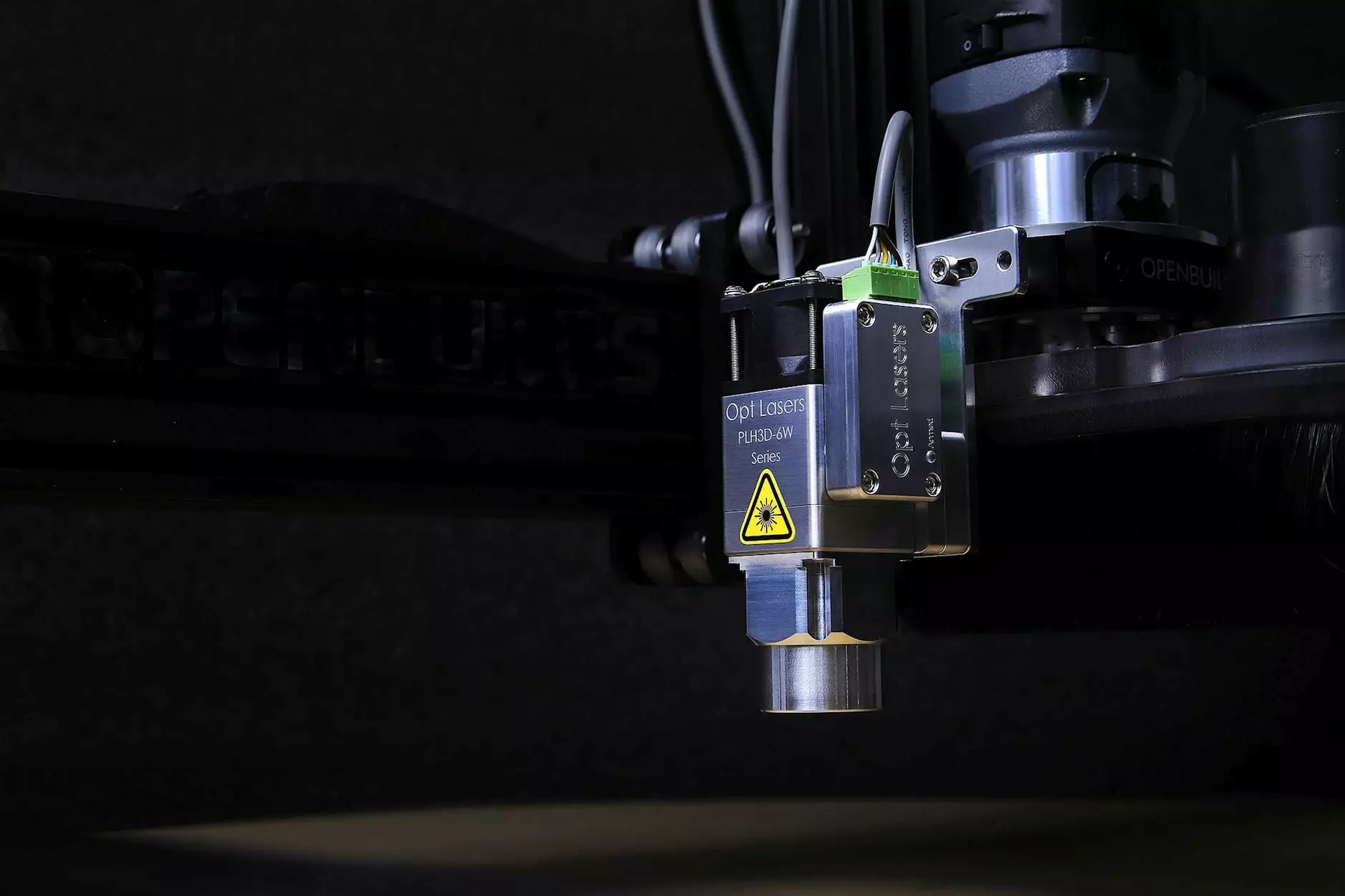
The modern manufacturing landscape is constantly evolving, and within this dynamic environment, CNC turning parts have emerged as a crucial element in the production of high-quality metal components. At Deep Mould, we delve into the significance of these parts and how they contribute to the efficiency and precision required in today’s industries.
What are CNC Turning Parts?
CNC turning parts refer to components that are produced using Computer Numerical Control (CNC) technology, specifically through a turning process. This manufacturing method involves rotating the workpiece against a cutting tool to achieve the desired shape and finish. CNC turning is known for its precision, efficiency, and ability to produce complex geometries, making it an essential technology for today's metal fabricators.
The Significance of CNC Turning in Metal Fabrication
CNC turning has transformed how metal parts are fabricated. Metal fabricators, like Deep Mould, utilize CNC turning for several reasons:
- Precision: CNC machines provide unparalleled accuracy, achieving tolerances as tight as a few microns.
- Efficiency: The automated processes reduce lead times and increase production speed, allowing manufacturers to meet tight deadlines.
- Consistency: Once a program is set, CNC machines can replicate designs with high fidelity, ensuring uniformity across batches.
- Complex Profiles: With CNC turning, it’s possible to create intricate designs that would be difficult or impossible to achieve with traditional methods.
Applications of CNC Turning Parts
The versatility of CNC turning parts has led to their widespread application across various industries:
- Aerospace: Used for producing components such as turbine blades, shafts, and structural elements.
- Automotive: Essential in manufacturing parts like brake components, gears, and engine components.
- Medical: Precision parts for surgical instruments, implants, and prosthetics.
- Electronics: Components such as housings, connectors, and heatsinks.
- Industrial Equipment: Custom parts for machinery, valves, and fittings.
Choosing the Right Metal Fabricator for CNC Turning Parts
When selecting a metal fabricator for your CNC turning needs, consider the following:
- Experience: Look for a fabricator with a proven track record and relevant industry experience.
- Technology: Ensure they use modern CNC machinery and techniques to produce high-quality parts.
- Quality Assurance: Ask about their quality control processes to ensure the components meet industry standards.
- Customization: A good fabricator should offer tailored solutions to meet specific project requirements.
- Customer Support: Look for a company that provides excellent support throughout the project lifecycle, from design to delivery.
Understanding the CNC Turning Process
1. Design Phase
Every CNC turning part starts with a design. During this phase, engineers create detailed CAD (Computer-Aided Design) models that define the specifications of the part. It’s essential to ensure accuracy and feasibility before proceeding to the next stage.
2. Setting Up the CNC Machine
Once the design is finalized, the CNC machine must be set up accordingly. This includes selecting the right cutting tools, determining the appropriate speed and feed rates, and loading the material onto the machine.
3. Machining
During the machining process, the CNC machine executes the programmed instructions, performing rapid rotations and precise movements to cut the material into the desired shape. The automation involved ensures that the part is produced efficiently and accurately.
4. Finishing and Quality Control
After the machining process, parts may undergo finishing operations such as polishing, coating, or additional machining to enhance their properties. At Deep Mould, our quality control team rigorously tests and inspects all parts to ensure they meet our high standards.
Materials Used in CNC Turning
A variety of materials can be utilized in CNC turning, depending on the application requirements:
- Aluminum: Lightweight and corrosion-resistant, perfect for aerospace and automotive applications.
- Stainless Steel: Highly durable and resistant to corrosion, making it suitable for medical and industrial uses.
- Brass: Often used for components requiring excellent corrosion resistance and conductivity.
- Plastic: Materials such as Delrin or Nylon can also be machined to create lightweight components.
- High-strength Alloys: Used in applications where durability and performance are critical.
Advantages of Using CNC Turning Parts
There are numerous advantages to utilizing CNC turning parts in your projects:
- Speed: Rapid production capabilities ensure that projects can be completed on time.
- Cost-Effective: Reduces waste and material costs due to precise machining.
- Labor Savings: Minimal manual intervention required, allowing for reallocating workforce resources.
- Technological Advancements: Constant improvements in CNC technology enhance the capabilities of CNC turning.
CNC Turning vs. Other Machining Processes
While CNC turning is highly effective, it’s essential to understand how it compares to other CNC machining processes:
- CNC Milling: This process uses a rotating tool to cut material. It is often employed for creating flat surfaces and complex shapes.
- CNC Grinding: Focused on achieving smooth surfaces and precise dimensions, often used in finishing processes.
- CNC Electrical Discharge Machining (EDM): This method is suitable for hard materials and complex shapes, producing parts through electrical erosion.
Future Trends in CNC Turning Technology
The future of CNC turning parts is bright, with several trends shaping its development:
- Automation: Increased use of robotics and automated systems will further enhance efficiency and precision.
- Integration of AI: Artificial intelligence will help optimize machining processes and improve predictive maintenance.
- Advanced Materials: Research into new alloys and composites will expand the capabilities of CNC turning.
- Sustainability: Efforts to reduce waste and energy consumption will become increasingly important in CNC manufacturing.
Conclusion: The Role of Deep Mould in CNC Turning
As a leading provider of CNC turning parts, Deep Mould is dedicated to delivering high-quality metal components that meet the diverse needs of various industries. Our commitment to using advanced technology, combined with our thorough quality control processes, positions us as a trusted partner in the realm of metal fabrication.
For businesses looking to leverage the advantages of CNC turning and acquire precision-engineered parts, Deep Mould stands ready to support your manufacturing goals. Our expert team is eager to collaborate with you, ensuring that your specifications are met with the utmost precision and care.
Get in Touch
If you’re interested in learning more about our CNC turning capabilities or would like to discuss a specific project, please feel free to contact us. Together, let’s create parts that drive innovation and quality in your industry!